高阶篇:4.2.2)DFMEA层级分明的失效模式、失效后果、失效原因
本章目的:明确失效模式、失效后果、失效原因的定义,分清楚层次关系,完成DFMEA这部分的填写。
1.失效模式,失效后果,失效原因的定义
这是FEMEA手册第四册中的定义。
1.1 潜在失效模式 (b)
潜在失效模式是指零部件、子系统、系统可能潜在地不能满足或者实现项目栏里描述的预期功能的状态。
识别与功能/要求有关的潜在失效模式。潜在失效模式应当用专业技术术语描述,不必描述成顾客能够注意到的现象。
一个功能可能有多个失效模式。如果一个功能被识别有大量的失效模式,则可能说明要求没有妥善的定义。
由于假设失效模式可能发生,但不是一定会发生,因此使用“ 潜在” 一词。
应当予以考虑潜在失效模式可能只在特定的运行条件(比如:热、冷、干燥、灰尘环境等) ,和特定的使用状态下(超过平均里程,不平的路段,仅在市内行驶等等)发生。
在确定了所有的失效模式后,分析的完整性可以通过对过往运行不良、关注点、问题报告和小组“头脑风暴”的评审来确认。
潜在失效模式也可能是上级子系统或系统的潜在失效模式的原因,或者是一个下级零部件的失效模式导致的影响。
有关不同要求的失效模式的例子,可以参见表Ⅲ.3。
英文原版如下:
1.2 潜在失效后果(C)
潜在失效影响(后果)是指由顾客感受到的失效模式对功能的影响。
根据顾客可能察觉和经历到的现象来描述失效影响。这里的顾客可以是内部顾客,也可以是最终使用者。如果失效模式可能会造成安全方面的影响,或者不符合法律条例,则应当清楚的说明这个问题;应当始终根据受分析的特定系统、子系统或零部件来进行说明后果。需要注意的是,在零部件、 子系统、 系统等级之间存在系统层次上的关系。例如:一个零件的断裂可能会引起总成件的震动,从而导致操作系统的中断。操作系统中断会使性能下降,最后引起顾客的不满。因此,就需要根据专业小组的知识程度,来尽可能的预测潜在的失效影响。
典型的失效影响可以根据产品或系统性能来说明。 表Ⅲ.4给出了表Ⅲ.3里的失效模式的影响。
英文原版如下:
1.3 失效模式的潜在原因/机制(f)
这部分信息可以被分为多栏,也可以合并成一个单独栏。
在开发FMEA的过程中,识别失效模式的所有潜在原因对后续的分析步骤是十分重要的。尽管有不同的方法(比如头脑风暴)可以用来确定失效模式的潜在原因,但还是建议小组着重于理解每个失效模式的失效机制。
1.3.1 失效模式的潜在机制(f1)
失效机制是指导致失效模式的物理、化学、电、热或其它过程。 需要注意,失效模式是一个“观察到的”或“外部的”影响,不应当把失效模式和失效机制,失效模式背后的实际物理现象,退化过程,或者导致失效模式的连锁事件相混淆。
在最大程度上,应当尽可能将每个失效模式的潜在机制简明、完整的列出。
对于一个系统,失效机制是一个跟随在零部件失效后面的错误的传递过程,从而导致系统失效。
产品或过程可能由于一个共同的失效机制,而有多个相互关联的失效模式。
确保过程影响被作为DFMEA过程中的一部分
1.3.2 失效模式的潜在原因(f2)
失效潜在原因是对设计过程如何允许失效发生的说明,应被描述为可以纠正、控制的问题。
潜在失效原因可能是一个设计或过程不足的显示,其结果是失效模式。
原因是指导致或激活失效机制的环境。
在识别失效潜在原因时,对特定的失效原因要使用简洁明了的描述,比如:特定的螺栓电镀会产生氢脆。不能使用模棱两可的用词,例如:设计薄弱,不恰当的设计。
在进行原因调查时,应关注于失效的模式,而非失效的后果。在确定原因时,小组应当通过讨论,来认为存在的原因会导致失效(即:失效模式的发生并不要求有多个原因) 。
通常来说,各种不同的原因每个都可能引发失效模式,从而导致了失效模式的原因的多个线索(原因分支) 。
尽可能的将每个失效模式/失效机制的每个潜在原因简洁、 完整的列出,以便可以对各个原因进行详细分析,进而采取不同的衡量,控制,纠正措施。
表Ⅲ.5显示的是表Ⅲ.3里的失效模式的原因举例。表内包含的失效机制,尽管并不要求作为FMEA表格的最小元素,但它显示了失效模式,失效机制和失效原因之间的联系。
在准备DFMEA时,假定该设计将被按照设计意图来制造、装配。经过小组斟酌,可以对以往历史数据显示的制造过程中的不足之处作例外处理
//作者认为初学者就解读FMEA手册关于这方面的定义有些困难,不妨先看看下面的内容。及自己去寻找些资料,更加有利于DFMEA的学习。关于定义的解读,最重要的两点:
①失效模式,失效后果,失效原因的层次关系;
②三者均需要专业术语的描述。参见
2.失效模式,失效后果,失效原因的解读
2.1 Potential Failure Mode (潜在失效模式)
失效模式包括了6种状况:
1)Loss of Function;功能失效;
2)Partial or Degraded Function;功能不全面或衰退;
3)Intermittent Function间隙性无功能;
4)No Function When Required;没有客户要求的功能;
5)Functions When Not Required;非客户要求的多余功能;(实际设计中出现非客户要求的多余功能,客户一般不会抱怨,但出于简化产品及节约成本考虑,可以加入。
6)Unintended Function (Performs a different function)非预期功能(表现为另外一种有害功能)。
//总而言之,这6种状况都是没有符合要求而产生的。
每种失效模式必须对应一种要求。//即没有凭空诞生的失效模式。
潜在失效原因不是潜在失效模式。//层级别弄错。
所有的要求都有一种或以上的失效模式。
所有的失效模式在质量预防历史或质量预防数据库中已经定义。//这个要看行业和公司的积累了。
2.2 Potential Effects of Failure(潜在失效后果)
1)Causes MUST NOT be Listed as EFFECTS.原因不能列为后果。//层级关系,因果关系不要混淆。
2)Severity Ratings MUST attach to each Effect.严重度评级必须附加到每个失效后果。
失效后果可以考虑:
①政府规定;
②客户需求;
③标准;
④系统接口;
⑤包括已知投诉/召回;
⑥安全性;
⑦可装配性/可制造性;
⑧可服务性;
⑨包装/运输/交通;
2.3 Potential Cause of Failure(潜在失效原因)
1)潜在失效原因被定义为设计薄弱部分的象征-即失效模式的推论;
2)至少,所有第一层级的原因必须被定义。第一级原因是一个故障模式的直接原因;
3)独立原因分别记录和评价;
4)过程原因(PFMEA中的事情)不应该被收录在DFMEA中;
5)失效原因可描述为能被确定或控制的特征。
6)分析由于噪音因素导致失效原因,需要由工程质量操作系统管理EQOS - Engineering Quality Operation System。
//第六点作者也不知道什么东西。
3.层次的划分(重要)
对于层次的了解,下图最能体现:
※该层失效模式是高阶系统的失效原因,或较低阶零组件的失效后果
注:说白了,失效模式,失效原因,失效后果其实是一回事,只是针对的层级不同而已。
理解了上面这张图,那么可以说DFMEA理解了大半了。
4.为何要分层级
为了更加系统、清楚、简便的分析,得出最终的失效原因。
在 高阶篇:4)可靠性设计 中的引子中有提到古英格兰有一首著名的名谣:“少了一枚铁钉,掉了一只马掌,掉了一只马掌,丢了一匹战马,丢了一匹战马,败了一场战役,败了一场战役,丢了一个国家。”
若是从国家灭亡的原因中直接去寻找那一枚铁钉,无异于天方夜谭。但如果先从国家灭亡的原因中找出战役,再找出战马,再找出马掌,最后找出铁钉,确是简单的多,也有条理可寻。
5.填写步骤
5.1 填写失效模式(重要)
潜在失效模式是依据要求而定的,思考及填写方法如下图所示:
重点在于1.2.3条失效模式的分析。
//如果一时之间找不到合适的专业用语描述失效模式,那就笼统写xx功能失效/衰退等,当然最后还是要转换为专业用语才是符合标准的。
5.2 填写失效后果
所谓的失效后果,即上一个层级的失效模式;
如下图(QFDII中图):
零件D的上一层级为膨胀阀阀体部件。在产品在xx条件下正常工作的条件下,零件D失效模式为鉍金属弹簧断裂,其失效后果就是膨胀阀阀体部件的失效模式,为阀体部件锁死。
5.3 填写失效机理(failure mechanism)
其实手册中也明确提出了,比起失效原因更加应该注重失效机理。(it is recommended that the team should focus on an understanding of the failure mechanism for each failure mode.)
但很多时候我们会往往忽视失效机理的描述,究其原因其一是失效机理的描述并非强制性的,其二是手册中的示范表格没有给出失效机理的一栏。(这可以说是很大的不足)
但机理的描述往往能更加详细明确地找到失效原因。
描述失效原因之前请描述,
5.3.1 观察这个零部件与其他部件之间的关系(方块图)
这个也是方块图的作用之一。
5.3.2 依据这个关系描述失效机理
方块图给出了零部件之间的作用关系,就可以描述外因。那么,一个和多个外因的作用下,零件失效。这就是失效机理的描述。
5.3.3 依据失效机理给出失效原因
失效机理可以描述零部件与其他零部件地关系;(方块图给出)
失效原因只能描写内部因素,如手机摔地上摔碎,请描述手机内部结构问题,而不要描述地板太硬的问题。
5.4 填写失效原因
所谓的失效原因,即下一个层级的失效模式;
但需要这注意,因为要求的不同,并非所有的下一个层级的失效模式都是原因。所以,明确的分析需要QFDII支持。如下图所示(QFDII中图):
在要求①着屏下,组件B的失效原因肯定与零件D及组件C都有关系。但在要求②重现率下,组件B的失效原因只能与零件D有关。
若不是,则需要同步更改QFDII和DFMEA。这也是反复的修正也是完善产品设计的方法。
5.5 这三步填写完成的组件B的DFMEA如下(示意):

5.6 再举一个零件的例子
零件D的QFDII如下
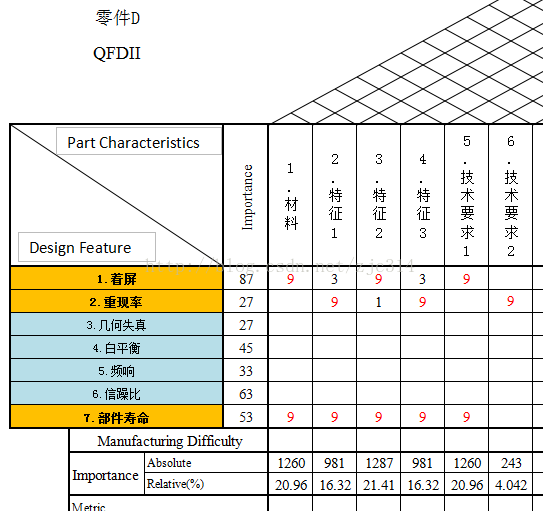
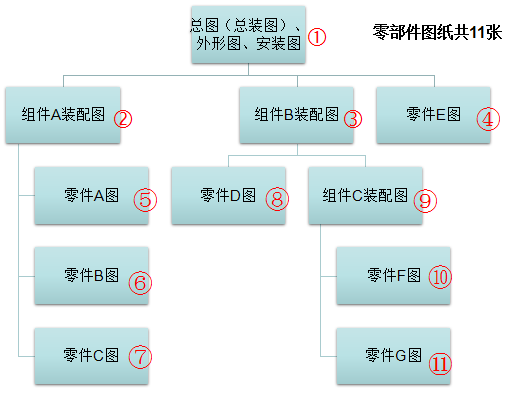
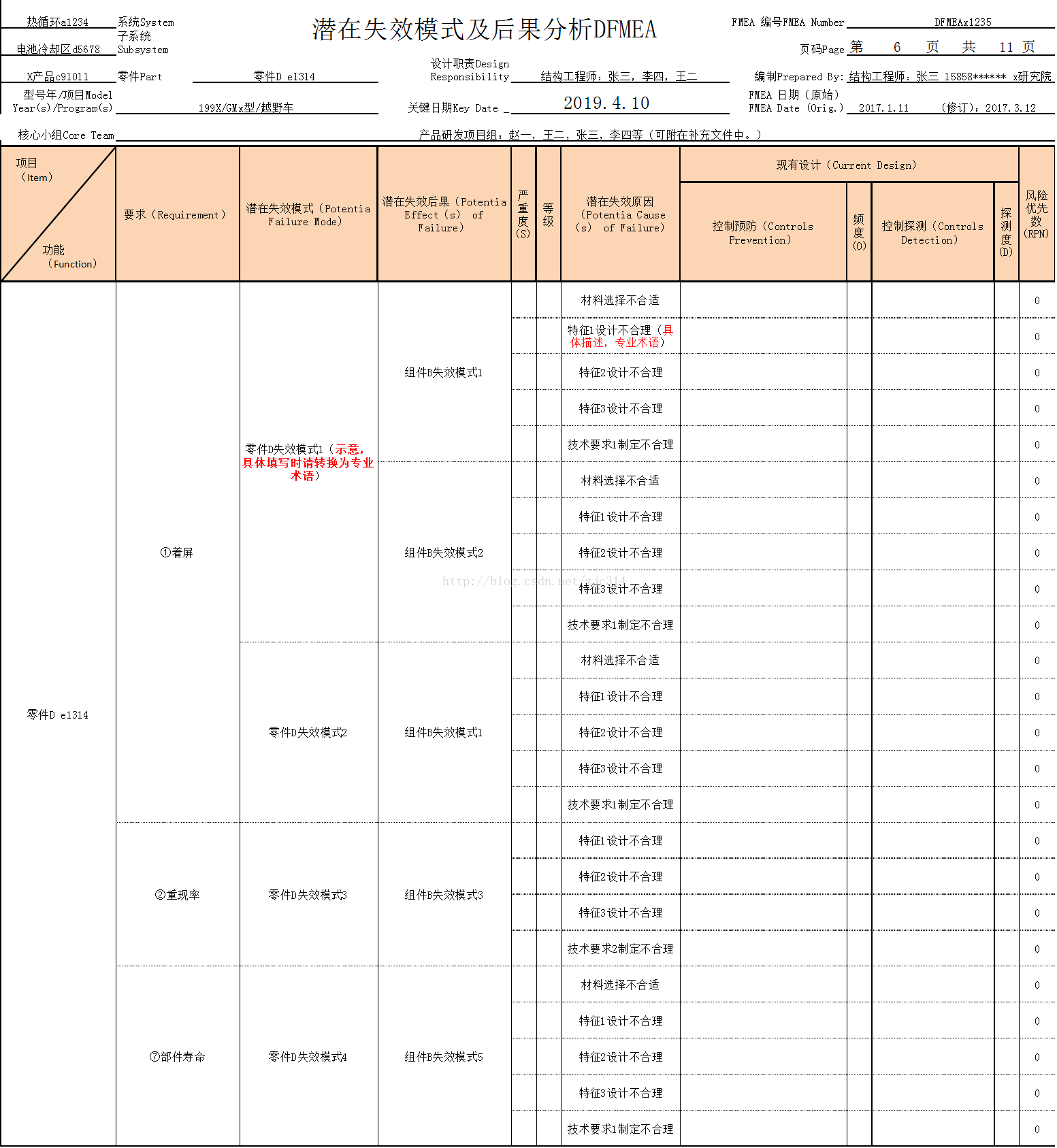
5.7 填写完成
6.争论点
6.1 一种失效模式可否对应多种失效后果
例子1:
零件D为有焊点的零件,失效模式是焊点设计不当导致的焊接不良。那么失效后果1(组件B失效模式1)为断路,功能失效;对应的失效后果2为组件B间歇性工作(由于接触不良导致,这也是可能的)。
例子2:
6.2 当一个失效模式对应多个失效后果时,是否只填写最严重的那个即可。
有些文章中写道,分析故障后果时,应尽可能分析出故障的最终影响,即最严重的影响。
FMEA手册中关于严重度S的定义时有这样描述:Severity is the value associated with the most serious effect for a given failure mode. 。所以有人就认为,当一个失效模式对应多个失效后果时,填写最严重的那个即可。
但作者认为当一个失效模式对应多个失效后果时,需填写所有的失效后果。
原因在于:
1)FEMA手册中描述:产品或过程可能由于一个共同的失效机制,而有多个相互关联的失效模式。
A product or process can have several failure modes which are correlated to each other because of a common failure mechanism behind them.
2)手册中的严重度s是衍生的评价手段,失效后果的填写与否与评价与否并非绝对关联,不是说放过那些较为轻微的失效后果。
3)当放过的那些不是最严重的失效后果发生时,就不能追溯原因了;